A new generation of startups are determined to disrupt the construction industry. Innovative early-stage ventures are striving to automate homebuilding with the use of industrial-size 3D printers. Applying 3D printing technology to home construction, they contend, is faster, cheaper and more sustainable than traditional methods.
Could 3D printing help address the problem of severe housing shortages that have led to soaring home prices across the U.S. and many parts of the western world? And will it be the solution that provides adequate, dignified and affordable housing in developing nations?
3D Printing Explained
3D printing, or additive manufacturing (AM), is a process of making three dimensional objects from a digital file. In essence, following digital blueprints, machines deposit layers of material (plastic, fiberglass, metal, concrete, etc.), one on top of the other, eventually producing three-dimensional objects or structures. The biggest difference between a typical 3D printer, and one used in home construction, is size. Those used to build homes are giant and robust machines that can print coarse material such as concrete.
Scaling 3D Printing for Home Construction
For years, innovators have be working on the most effective way to scale 3D printing technology to produce industrial-sized structures like homes and buildings. While many of today’s industrial printers still resemble smaller 3D plastic printers (they’re simply on a much larger scale and fed with concrete), there is a lot of variation with respect to the technology’s implementation. Some printing companies are opting to print out panels in factories, then transport them to, and assemble them at, their final location (similar to pre-fab buildings). Others believe the optimal solution is to print homes on site, thereby saving on added transportation costs. Further variables companies are playing with include: best composite materials to use, how to improve aesthetics of finished surfaces, and how to incorporate additional components including structural reinforcement, insulation, electrical, plumbing, roofing, etc. Since 3D printing homes is still relatively new, we’ll no doubt see a great deal of change and innovation as the race to optimize building methods continues.
6 Amazing 3D PRINTED HOUSE Projects in 2020
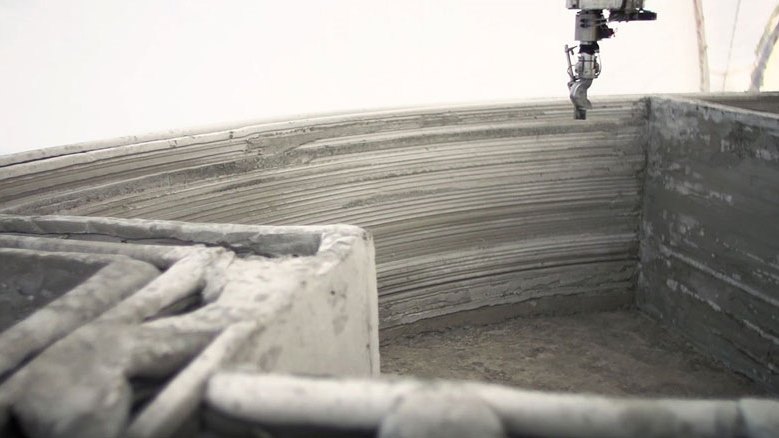
The Benefits of 3D Printing Homes
As 3D printing technology and building methods continue to evolve, we are beginning to see a variety of distinct advantages of 3D printing homes. In particular, 3D printed homes can be built much faster than in conventional construction. They reduce the need for costly skilled labor in various trades and eliminate errors which leads to much less waste material. Cumulatively, this brings down the overall cost of construction. In addition, 3D printing offers far more design options than were previously possible.
Much Faster
Building a 3d printed house is much faster than conventional construction. Once up and running, some systems canĀ print a meter in just secondsĀ using data from integrated design models. So a 3D printer can build the foundation and walls of a house in as little as two days versus weeks or months with traditional framing methods. And while there are a lot more components that go into a house (utilities, roofing, windows and doors, interior and exterior finishings, etc.), complete start to finish construction time can be reduced by months.
Reduces Waste
Proponents of 3d printing homes note that the technology is far less wasteful than the concrete forming and wood framing used in traditional construction. 3D printing houses could save huge quantities of scrap wood, metal and other discarded construction materials that are dumped into landfills every year. Its estimated that just one conventionally constructed house produces as much as two to three tons of waste material. But with 3D printing, you don’t get the unnecessary waste. With 3D printing, you only print what you need. Building material is laid precisely. Plus slots and spaces for services and fixtures are already built into the structural design, eliminating the need to cut and drill and waste further material.
Addresses Problem of Skilled Labor Shortages
Currently, there is a lack of young people entering the trades. Home builders are struggling to find enough skilled workers to meet housing demand, which is a major contributor to soaring home prices. So the introduction of 3D printing in construction, couldn’t have come at a better time. 3D printing reduces the need for human labor thanks to a number of factors:
- 3D printed homes do not require large teams of carpenters and laborers that are typically needed to form the foundations and put up the walls in conventionally built homes.
- 3D printers can work around the clock. They don’t require lunch breaks, weekends or statutory holidays, which further reduces the size of the crews needed.
- 3D printed homes integrate the services of additional trades (electrical, plumbing, heating, cooling, roofing, etc.), into the structural design. This eliminates errors and the need for additional labor (cutting slots, drilling holes, installing suspension and support systems, etc.).
All of these factors have a tremendous impact on reducing a developer’s labor expenses, one of the biggest input costs in home construction.
Reduces Costs
All of the above benefits of 3D printing – speed, reduced waste, reduced need for skilled labor – bring the cost of home construction, and ultimately home values, down. And the trend in falling costs can only be expected to accelerate as the nascent technology transitions from pilot projects to full-scale commercial use. Innovative new companies, seeing the huge potential, are incessantly working to reduce costs further, deploying more efficient printer designs, experimental concrete mixes, as well as creative new home designs that break the rules of traditional building.
Offers More Design Possibilities
One of the most exciting benefits of 3D printing homes, is it opens the door to a greater variety of architectural designs. With the advent of 3D printing, innovative design won’t be limited to large-budget private or publicly funded buildings. Traditionally, home building has largely been limited to squares and rectangles due to financial constraints. But with 3D printing technology, its now possible to lay structures with curvilinear forms. Not only are such designs much more durable and sustainable than squares and rectangles, but they allow for far more creativity and human expression. Future home designs may be as limitless as the imagination.
Criticism and Limitations of 3D-Printed Homes
All too many advocates of 3D printed homes are guilty of painting an overly simplistic picture of a magical technology that prints homes from start to finish. But this is far from reality. So while its easy to be persuaded by all the proposed benefits of 3D printing homes, its also important to be cognizant of the criticisms that have been raised by players within the construction industry. Because with any new idea, there are often big gaps between theory and real-world application.
Many More Components/Costs In Home Construction
3D printers simply create the structureĀ – one of many components of a home. You can 3D print the foundation and walls, but you canāt print pipes, wires and other installations. 3D printers will not paint your walls or furnish your kitchen. You still need to coordinate all the different trades in order to incorporate: plumbing, heating and cooling, electrical, roofing, interior finishing, furnishing, landscaping, etc. Even 3d printed walls themselves, often look rough and unfinished, requiring post-processing just like in traditional construction. So when you not only count the 3D printed framework, but also the labor and dollar cost of all the additional elements, the actual savings is generally much less than most anticipate. A home after all, is worth multiples more than the simple cost of the walls and foundation.
Optimistic Cost Estimates Not Necessarily Accounting for Shipping and Maintenance
Certain media campaigns have been somewhat disingenuous about all-in costs of producing 3D printed homes. In their cost projections, they fail to mention the less intuitive, but equally important, hidden costs of shipping and maintaining the machines themselves. Industrial-scale 3D printers can cost thousands of dollars to move. And the material they deal with is coarse and heavy and will result in a great deal of wear in tear that is unavoidable once they start working in larger volumes. This in turn, means you will need technical expertise on site. Not just programmers, but actual skilled trades that can repair and change out mechanical components. So when you hear some of the fluffy marketing campaigns for 3D printed houses, those that claim “it’ll cost $10,000 to build a house,” take these projections with a grain of salt. How many hidden costs are they conveniently ignoring? Even though costs will certainly come down over time (with continued innovation and as we scale up to multi-unit projects for commercial production), the current cost of 3D printing homes may not be as low as first anticipated.
How Do You Reinforce 3D Printed Concrete Structures?
Concrete, as strong as it is in most applications, needs reinforcement of some type so it doesn’t crack over time. The physical and mechanical properties of concrete are quite durable in a compact form, but when you extend it out over a large area, it’s tensile strength doesn’t hold up. This is where rebar comes in – for reinforcement. But how do you integrate the labor intensive task of installing rebar, with the automation of 3D printing? This poses one of the big challenges right now. How to effectively and efficiently reinforce 3D printed concrete? As such, there is still a technology gap to overcome before a truly automated 3D printing process is able to construct larger, multistory structures.
Permitting Challenges
While there are a lot of reasons to be enthusiastic about 3D printing homes, everyone has to understand that there are still numerous permitting challenges that have to be overcome. 3D printing, after all, affects the overallĀ construction process. Not only does it impact the execution of the foundation and walls, but it influences the planning and permitting for all of the other trades. A parallel can be drawn to manufactured and modular homes. While they’ve been around for decades, it took some time to sort out the standards and laws that regulate their quality and construction. The same will be true for construction with 3D printing technology. It is still in the very early stages of the regulatory process, so mass adoption may not be as imminent as some would have you believe.
That said, permitting is more of a hurdle to overcome than an indelible limitation. Case in point, a firm named PERI (a market leader in formwork and scaffolding systems), has already attained government certification for a 3D printed home they built in Beckum, Germany. This makes them the first 3D printing company to attain certification under a national government’s building regulations. And considering it was done in Germany, a nation known for very stringent building codes, this has been a momentous milestone for the budding technology on the whole.
Still Doesn’t Address Main Contributors to High Home Prices – Land Costs and Regulatory Fees
3D printing does little to address the main contributors of escalating home prices in many jurisdictions – land scarcity and uneconomical regulatory fees. Regardless whether land shortages are a result of real demand in densely populated urban areas, and/or due to artificial scarcity thanks to burdensome government regulation (permitting, land use bylaws, building codes, safety codes, environmental bylaws, etc.), there is a marginal benefit of reducing construction costs in municipalities with high land and regulatory costs. As promising as 3D printing is, it isn’t a panacea for land scarcity, government bureaucracy and red tape.
Inevitable Growing Pains and Hurdles Yet to Overcome
While there are a lot of justified criticisms pertaining to 3D printing’s limitations, and a lot of hurdles yet to overcome, 3D home printing still has all the hallmarks of a disruptive technology. The benefits that automation and digitization bring to homebuilding, particularly with regard to speed and cost, offer too much promise for industry leaders to ignore. Which is why innovative companies are starting to ink contracts for planned construction projects. A hypothetical idea just a decade ago, 3D printed homes are now moving beyond the pilot stage and into commercial production.
Sure there will be growing pains, mistakes, costly setbacks and expensive do-overs, but these are the necessary steps in advancing any new technology. The learning curve is going to take some time. And that goes beyond the 3D printing technology itself. Construction trades, contractors and engineers also need to learn entirely new processes in order to effectively integrate with 3D printing technology. But these yet unforeseen challenges can and will be overcome, and it won’t be long until we start to reap the benefits of 3D printing in home construction.